- COMPANY
Valmet Automotive EVS Oy (https://www.valmet-automotive.com/)
- SEMINAR’s focus
To conceptualize an efficient process for moving components from a warehouse to the production line (internal logistics).
- DESCRIPTION
Valmet Automotive is a leading European manufacturer of electric vehicle battery systems, convertible roof and automotive kinematic systems (including electric vehicle charging flaps and active spoilers) for OEMs, and one of the largest vehicle contract manufacturers in the world.
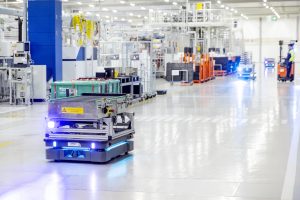
Strategically, Valmet Automotive focuses on electromobility through the development and manufacturing of battery modules and packs for electrified vehicles. The activities in the company are organized in three business lines: Vehicle Contract Manufacturing (VCM), EV Systems (EVS) and Roof & Kinematic Systems (RKS). The company has locations in Finland, Germany, and Poland. Since its founding in 1968, Valmet Automotive has produced 1.8 million vehicles at its plant in Uusikaupunki, Finland. Valmet Automotive also operates two battery systems plants in Finland (Salo, Uusikaupunki), and one in Germany (Kirchardt). The automotive roof and kinematic systems are manufactured in a plant in Zary, Poland. Valmet Automotive is certified CO2 neutral in its own operations since January 1, 2022, by the certification institute DNV. The company’s gross sales in 2023 amounted to EUR 2.2 billion (net sales EUR 531 million).
- CHALLENGE
A battery production line is comprised of a series of workstations. Each station performs a specific operation and the product is processed step by step as it moves along the line in a pre-defined production sequence.
When a station requires replenishing of the components the operator requests those components from the warehouse. As the result of this request the material should be moved from the warehouse to the production line. For each station the process to replenish the components is repeated constantly during the working shifts.
To achieve the goal to replenish the components, first the material has to be repacked in the warehouse and this process is manual. Each work station requires different components and therefore there are different needs for the repacking. The re-supply to the workstation must be done efficiently to not stop the production line. It is worth noticing that each workstation consumes its components at different rates, and it requires different time and effort to be re-supplied from the warehouse.
Re-supplying the components requires for each workstation manual labor, as the material must be repackaged from how they are received from the supplier to a format that suits the specific workstation. The repackaging is performed in the warehouse.
Resupplying individual workstations can be improved in the way the material is delivered to the production line. There are different factors to consider when repackaging and delivering the material to the production line, to mention a couple: material should be delivered in the right quantity and at the right time, the material should be positioned correctly in the work stations, the material should be requested by the production line from the warehouse, there is a handling of risk materials, different packaging formats, and when manual labor is involved it is also fundamental to avoid accidents, etc.
There is an interest to improve the packaging and delivery of material from the warehouse to the production line with an efficient approach. Therefore the aim of this session is to explore concepts to deliver material components from the warehouse to the production line and the different workstations more efficiently. It is important to notice that the persons at charge of the logistics of material and the production line, despite of working in the same location, are in different areas and have different processes.
Tasks for the session
- Discuss processes to improve internal logistics processes
- Find ideas how to to deliver material components to the different workstations in the production line more efficiently
Outcome
- Set of list of ideas on how the new processes could be implemented
- Concepts to be discussed with the company on how they can implement certain processes in the future.
- DAY and TIME
Monday May 20, from 9:00 hrs to 15:40 hrs
- SEMINAR LOCATION and TENTATIVE SCHEDULE:
Facilities at Valmet Automotive EV Power Oy.
Address: Joensuunkatu 7 C, 24100 Salo, Finland
Schedule:
- 9:00 – 9:40 Leave from UTU to SALO
- 9:40 – 10:00 NDA signature + Welcome
- 10:00 – 10:30 Presentation of the challenge
- 10:30 — 11:30 Visit Plant
- 11:30 — 12:00 Lunch
- 12:00 – 14:00 Team work
- 14:00 – 15:00 Outcomes
- 15:00 – 15:40 Return to UTU
- ENROLLMENT
Important NDA must be signed to be allowed to enter the production plant and participate in this seminar session.
Please enroll to the seminar session by filling the following form: https://link.webropol.com/ep/valmentautomotive
The enrollment closes on Thursday May 16th.
- PRE-ASSIGNMENT
To prepare ourselves and enrich our conversation during our Industrial Seminar session with Valmet Automotive EV Power, Oy , we should prepare ourselves by working on two pre-assignment tasks. Please submit the report of your pre-assignment by Friday May 17th at 12hrs. Hence we have time to share the pre-assigment to the company representatives.
You can find the instructions of the pre-assignment following this link.